Fazendo uma analogia, se o motor é o coração do carro, a carroceria é o seu corpo.
A carroceria é a parte do veículo mais difícil de ser projetada e desenvolvida, pois acumula vários requisitos que devem ser atendidos simultaneamente:
– Estilo
– Aerodinâmica
– Resistência a “flexo-torção”
– Deformação progressiva e direcionada da estrutura no caso de forte impacto, absorvendo a energia cinética do veículo e protegendo seus ocupantes no habitáculo/célula de sobrevivência
– Ser leve
– Ter proteção anticorrosão
– Garantir espaço e conforto aos ocupantes
– Vedação do habitáculo contra poeira, água e vazamentos de ar
– Circulação e renovação de ar eficiente
– Freqüências naturais que evitem ruídos ressonantes desagradáveis
– Estrutura que absorva as vibrações do conjunto motriz e das suspensões
– Facilidade de ser manufaturada
– Facilidade de manutenção e reparos
Hoje praticamente a totalidade dos carros de passageiros adota a estrutura monobloco da carroceria, consistindo da união de vários elementos de chapa de metal moldado por estampagem, com seções ocas e espessuras entre 0,7 e 1 milímetro.
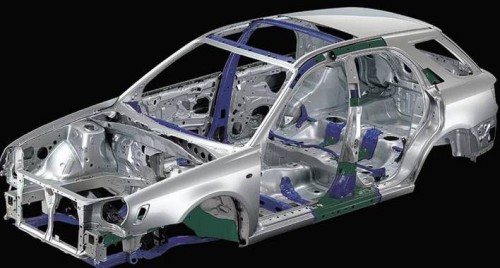
Nas regiões de maior resistência de junção, as chapas de metal sobrepostas podem atingir espessuras de até 3 mm. Os elementos são unidos basicamente por soldagem com aproximadamente 5.000 pontos caldeados, formando a chamada armação. As partes externas como portas, pára-lamas e coberturas são aparafusadas para facilitar a montagem e as manutenções e reparações. A carroceria monobloco é a mais eficiente em termos de custo-benefício.
A primeira surgiu no Lancia Lambda, em 1922, mas foi a partir da década seguinte que começaram a se popularizar, caso do Opel Kadett, de 1936.
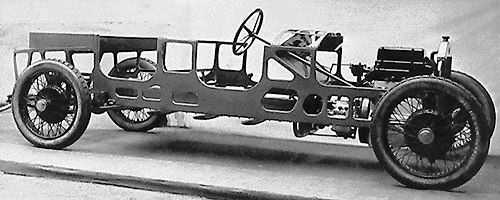

Uma das carrocerias mais eficientes em termos de resistência à torção e flexão, simultaneamente, certamente foi a do Porsche 911 Targa, em 1967, se perpetuando até os dias atuais.
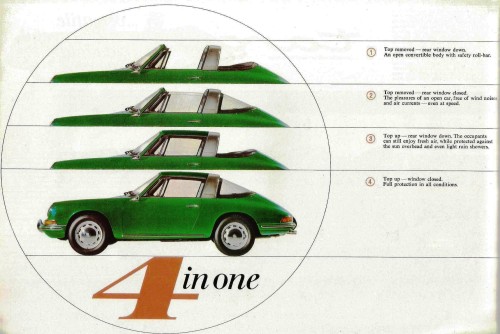
A genial idéia do Targa — nome usado em alusão à corrida de estrada Targa Florio, na Sicília, entre 1906 e 1977, com interrupções devido às duas guerras mundiais, e onde a Porsche foi vitoriosa várias vezes — surgiu da necessidade de vender 911 conversível no mercado americano que atendesse às crescentes normas de segurança nos EUA. Há menos de um ano foi lançado o 911 Targa de terceira geração, baseado no 911 de sétima geração, o 991, de novembro de 2011.
Outra estrutura básica de carroceria é a armação de tubos em treliça, utilizada em veículos esportivos e em carros de corrida. Esta construção é muito difícil de ser manufaturada pois os tubos em diferentes tamanhos e ângulos não são adequados para a soldagem automática robotizada. Normalmente esta estrutura excede os valores de resistência das carrocerias monobloco de maneira geral.
Uma estrutura tubular notória em termos construtivos e de eficiência foi a do Mercedes-Benz 300 SL, começando em 1954.
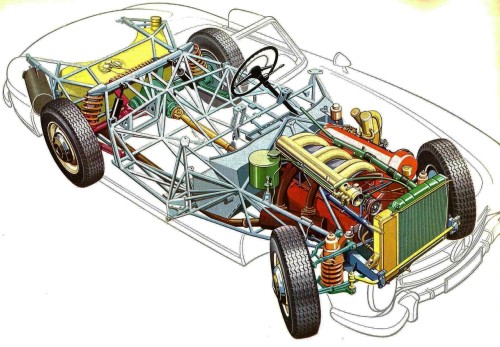
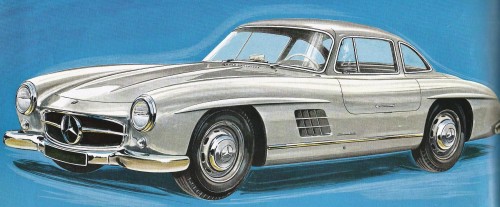
Outra configuração comum é o chassis tipo escada, separado da carroceria e utilizado na maioria dos veículos comerciais e fora de estrada. Esta construção é basicamente formada por duas vigas paralelas dispostas longitudinalmente e ligadas por vigas transversais e suportes em varias posições, suportando todos os esforços de transmissão de força, suspensões e carregamento. A carroceria instalada por cima, aparafusada, não tem outras funções adicionais neste aspecto.
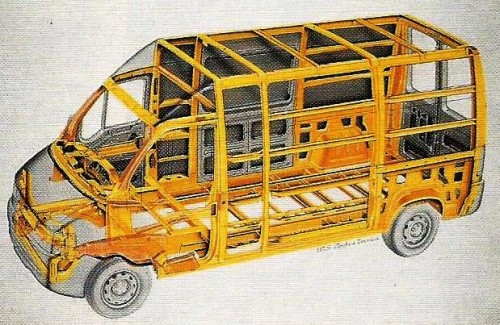
O projeto da carroceria, por conter muitas variáveis, requer invariavelmente o auxilio do computador para a determinação de toda a sua resistência estrutural.
CAE é a sigla para “Computer-Aided Engineering”, ou seja, engenharia auxiliada por computador, onde os engenheiros simulam um modelo virtual que correlacione totalmente com o modelo físico em termos de esforços solicitantes. A malha estrutural é gerada através de formas geométricas simples que pode ter 100.000 ou mais pontos de junção ou nós. O computador poderá então analisar o efeito das forças atuando com energia e direções diversas e nas espessuras e propriedades dos materiais. Neste procedimento altamente complexo, o computador fica habilitado a simular muitas condições de utilização do veículo e pôr em prática todo o processo do projeto estrutural.
Após toda a análise virtual ser concluída, é construído um protótipo físico que represente com mais de 90% de confiabilidade o projeto definido no computador. Este protótipo é testado severamente nas pistas de tortura dos campos de prova para certificar todo o projeto em termos estruturais e de movimentação da carroceria.
As rigidezes e as análises modais de vibração e freqüência natural são testadas em laboratório e modificadas apropriadamente quando necessário.
Testes de eficiência do projeto na proteção dos ocupantes do veículo em várias situações de acidentes são fundamentais. Os veículos são submetidos a vários testes de impacto, homologatórios/requisitos legais, para que as deformações progressivas da estrutura e a integridade da célula de sobrevivência seja preservada.
O alumínio e materiais compósitos estão gradativamente substituindo o aço na fabricação de carrocerias visando a diminuição de massa e aumento da resistência. Chapas de aço galvanizadas também têm sido introduzidas nos projetos para diminuir a corrosão.
Como curiosidade, a Chevrolet foi a primeira fabricante a oferecer uma carroceria de plástico de série. Foi em 1953 no Corvette, um dos maiores ícones dos veículos esportivos, e o material é usado até hoje, passados 62 anos.
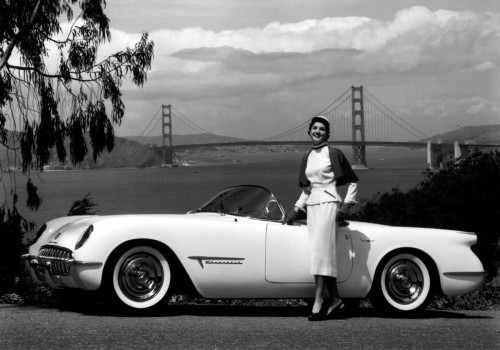
Outras curiosidades, o Audi A100 foi em 1982 o primeiro veículo no mundo a adotar chapas galvanizadas (zincadas) para minimizar a corrosão; o Audi A8 foi o primeiro sedã de grande porte a adotar a carroceria monobloco inteiramente feita em liga de alumínio. Isso foi em 1994 e continua até hoje.
E a melhoria contínua cria novos processos cada vez mais eficientes, tanto nos projetos quanto na manufatura dos veículos, ficando difícil vislumbrar o que vai ocorrer, por exemplo, nos próximos 50 anos.
Gostaria de ter a opinião do leitor a esse respeito.
Como fechamento da matéria, vale a pena citar a frase do acadêmico e filósofo inglês Roger Bacon (1219–1292):
“E irá ser possível construir veículos que se movimentam sem serem puxados por animais, propelidos por uma força inimaginável.”
CM
Créditos: VW do Brasil – fundamentos da tecnologia automobilística; arquivo pessoal do autor; bh-exotics.com; automania.be; pond5.com; favcars.com